Production plant
Absolute European excellence in the treatment of nanocomposed materials
WITEK has designed and built with the scientific supervision of CE.RI.COL a production plant dedicated to sanitizing products.
Years of research and experimentation took years to design a production line with the characteristics necessary to meet the technological needs suitable for the treatment of nanocompounds.
The processes related to the treatment of elements, from the ceramic filters that are on board the GearBOX to the coating of surfaces and materials inherent to sanitizing products, envisages a certified industrial principle. All the phases of this delicate process take place in our factory and this allows the total control of all the technological and industrial functions.
A “vision” that comes true …
A time-lapse on the complexity of assembling the production machine.
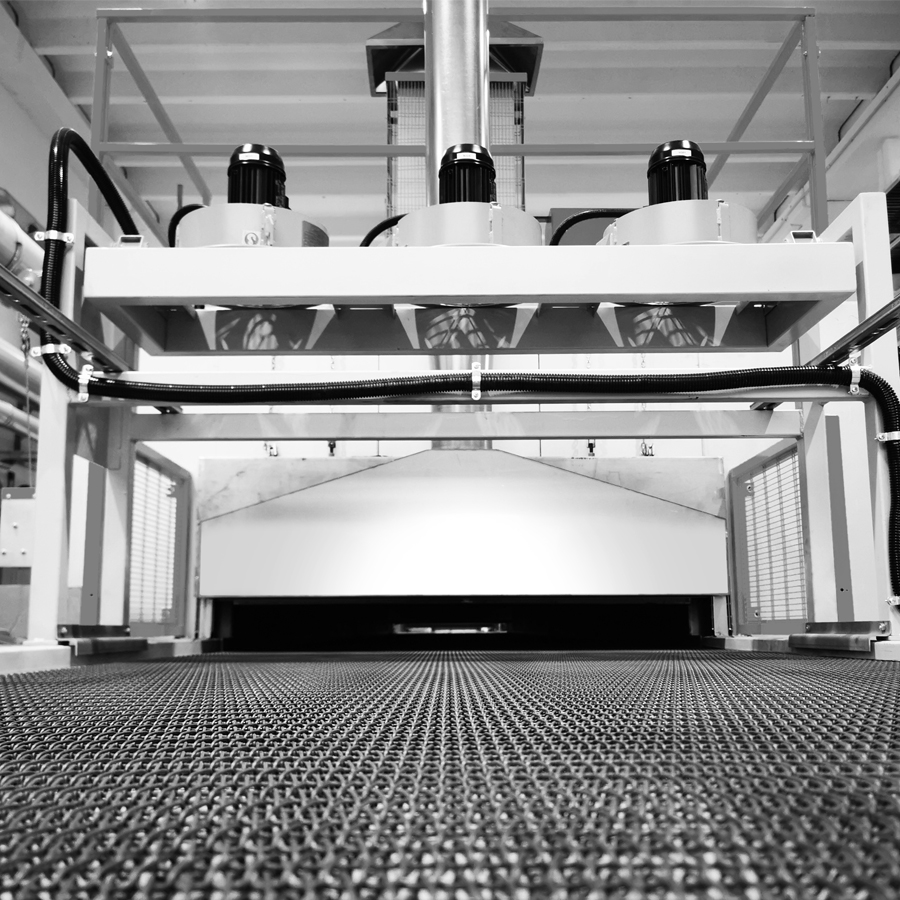
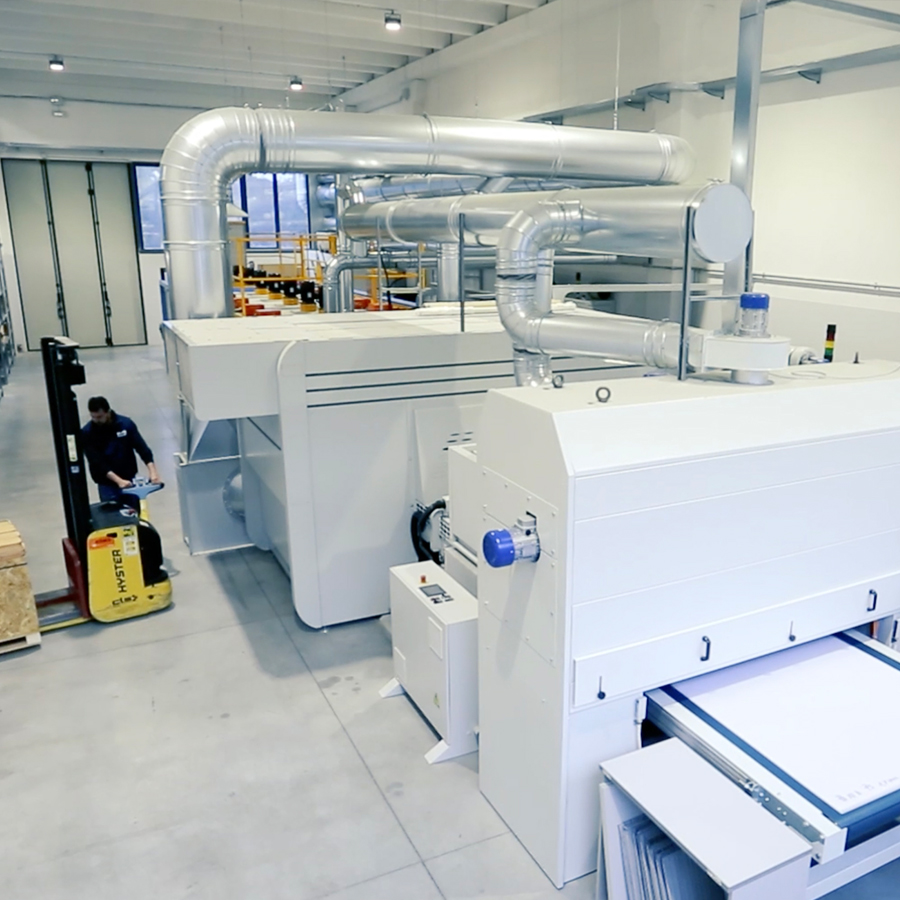
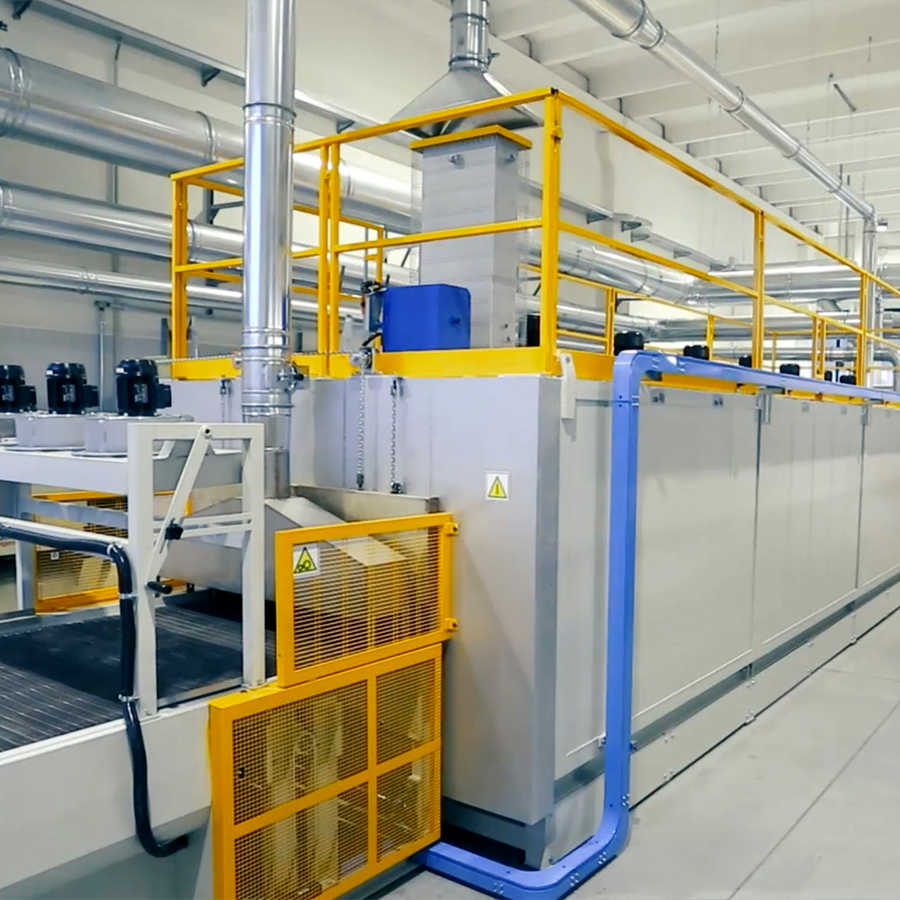
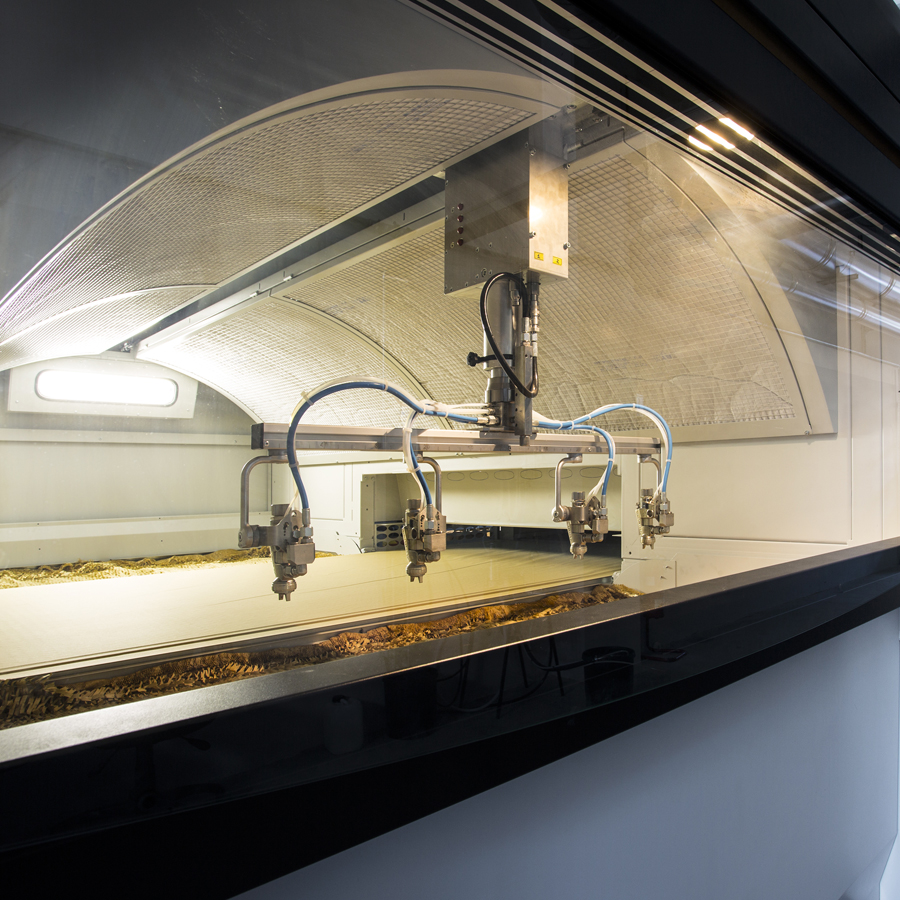
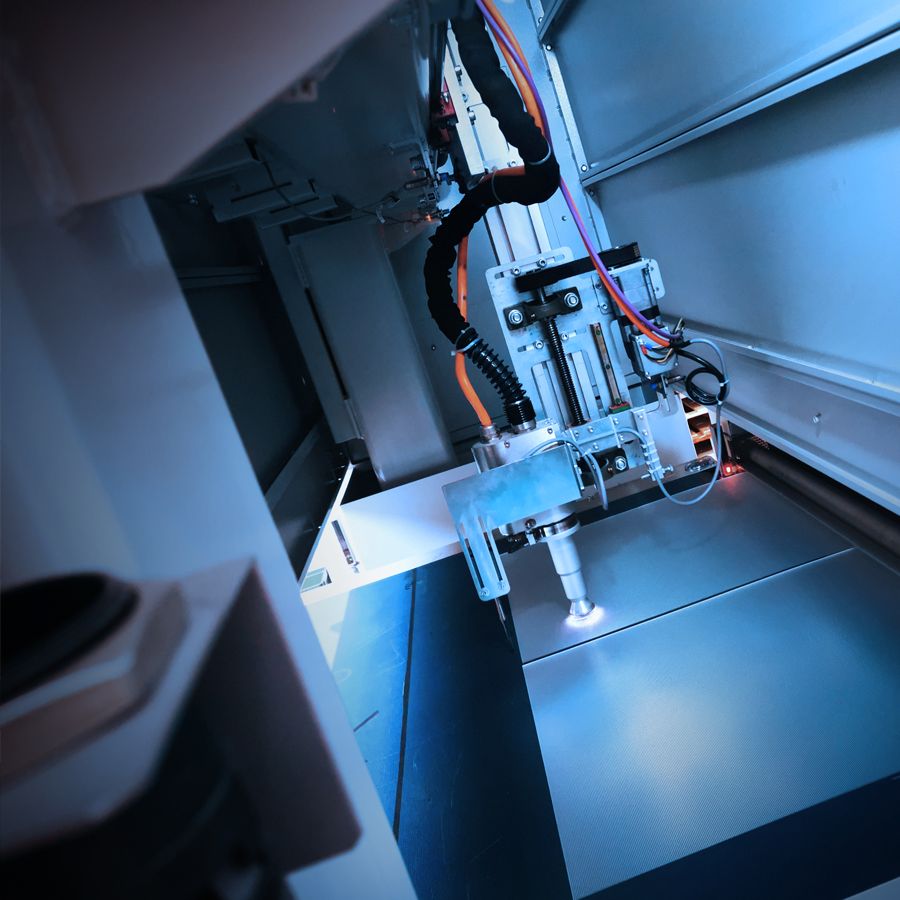
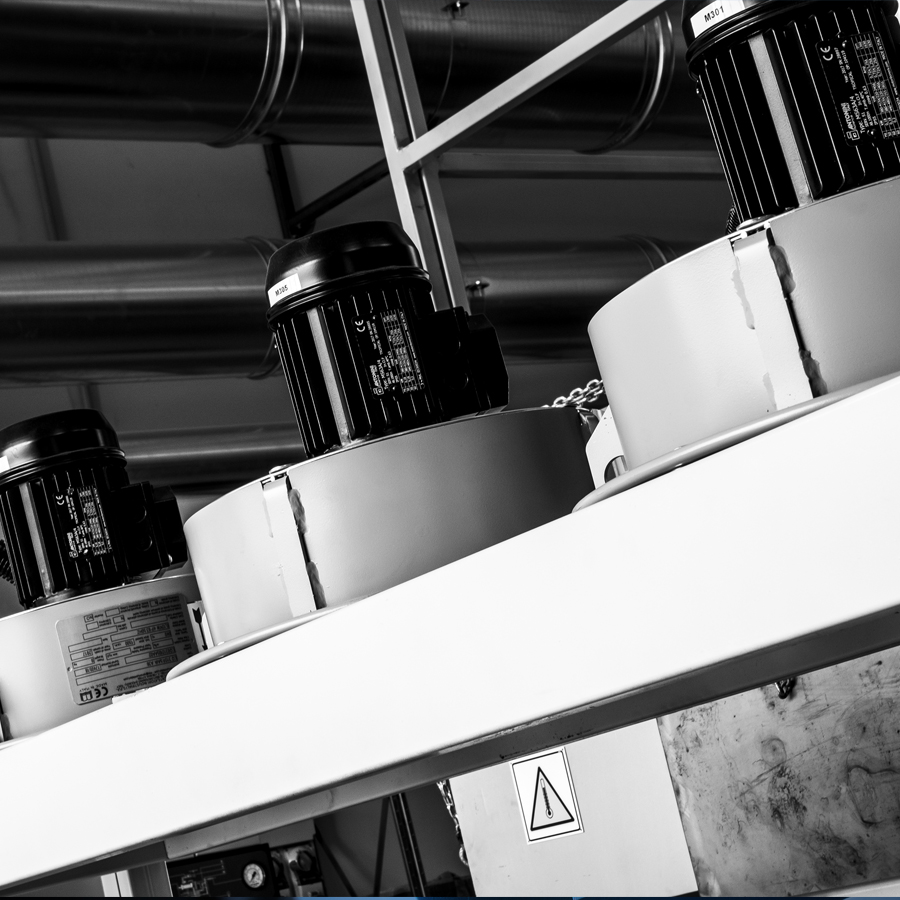
Process of coating
The nanomaterials are applied to the surfaces through a specifically developed coating treatment. The mixing and fixing of the nanocompound is a process that requires absolute knowledge of the chemical dosages and temperatures suitable for softening the surfaces in order to allow the nanotitanium to penetrate at a molecular level on the substrate to be treated.
The particular chemical composition of this substance, based on a special patented morphology of titanium dioxide and doping with silver and other elements, means that it is activated simply thanks to the action of visible artificial light, even in the absence of UV rays.
The phases of application of nanomaterials
The coating of nanomaterials on a surface takes place inside of a special machine through 5 phases:
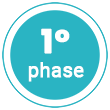
ACTIVATION OF NANOMATERIALS
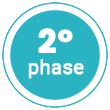
PREHEATING OF CERAMIC FILTERS
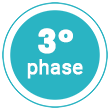
PROCESS FIXING
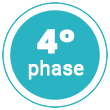
COOKING IN THREE PHASES IN SEQUENTIAL OVENS
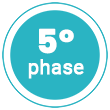
COOLING DOWN OF THE TREATED FILTER
Quality Control
The laboratory is equipped to perform tests to verify compliance with the European Directives 2014/35 / EU (low voltage) and 2014/30 / EU (electromagnetic compatibility) and with the following standards:
Incoming Quality Control IQC
The inspection of raw materials, which is mostly conducted by the subcontractor himself at its facilitiesaccording to Witek inspection standards and completed by both audits performed by Witek at the headquarters ofsubcontractor and through statistical checks upon receipt of the goods. Some sensitive elements of the product provide for a 100% control of the incoming goods.
IQC Activity:
- Inspection of the checklist; quality and quantity control of products
- Supplier evaluation
- Sample control or 100% of the incoming product
- Material quality inspection – visual or functional check according to the needs and type ofitem
- Implementation of the IQ quality control system.
In Process Quality Control System IPQC
The inspection of the in-line production process, which is performed by production personnel during the manufacturing process itself and which is based on monitoring key production measurements process quality parameters.
IPQC activities:
- Assembly inspection
- Statistical control techniques and control of deviations
- Process audit to ensure that processes comply with major standards and to identify any process improvements
Outgoing Quality Assurance OQA
OQA is the last procedure that is performed, before the product leaves our factory to the customer.
OQA activities:
Performing visual inspections and functionality tests. Our products require a 100% inspection leaving the factory to ensure the highest quality standards of the product.
- Update approved list of control checkpoints
- Samples based on approved standards
- Performing reliability assessments
- Generation of cancellation / warning and analysis reports